Comment améliorer durablement la performance sans en faire toujours plus ? Face à la complexité croissante des organisations, nombreuses sont les entreprises qui cherchent à gagner en efficacité, en qualité et en réactivité. Le lean management apporte des pistes concrètes pour repenser les façons de travailler et créer davantage de valeur. Encore faut-il bien en comprendre les principes.
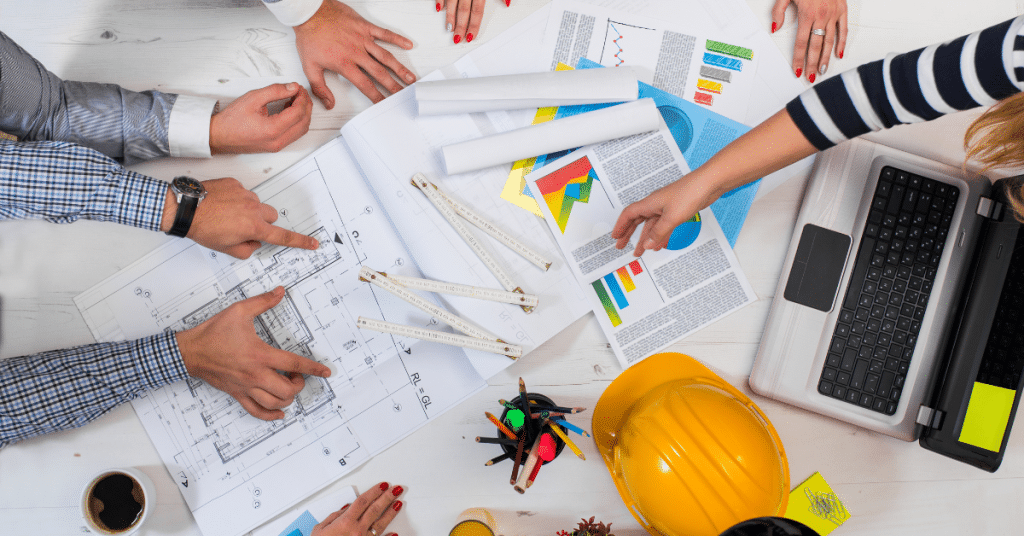
Le lean management est une approche d’organisation du travail qui vise à optimiser les processus d’une entreprise en réduisant le gaspillage, mais également en offrant davantage de valeur ajoutée pour le client.
Cette méthode encourage l’amélioration continue et cherche à réaliser des changements progressifs qui mèneront vers une meilleure efficacité et qualité des processus.
Quelles sont les bases du lean management ?
Originaire du système de production de Toyota, le lean a été développé au Japon après la Seconde Guerre mondiale par l’ingénieur Taiichi Ohno pour répondre à un besoin spécifique de production de véhicules tout en minimisant les stocks.
L’approche a été reprise par la suite en dehors du secteur automobile, notamment dans l’industrie et les services. Elle continue aujourd’hui d’évoluer et d’être adoptée par de nombreuses organisations issues de tous les secteurs.
Quels sont les 5 principes du lean management ?
Bien plus riche qu’une simple méthode de production, le lean recherche l’amélioration de la performance en s’appuyant sur cinq principes fondamentaux.
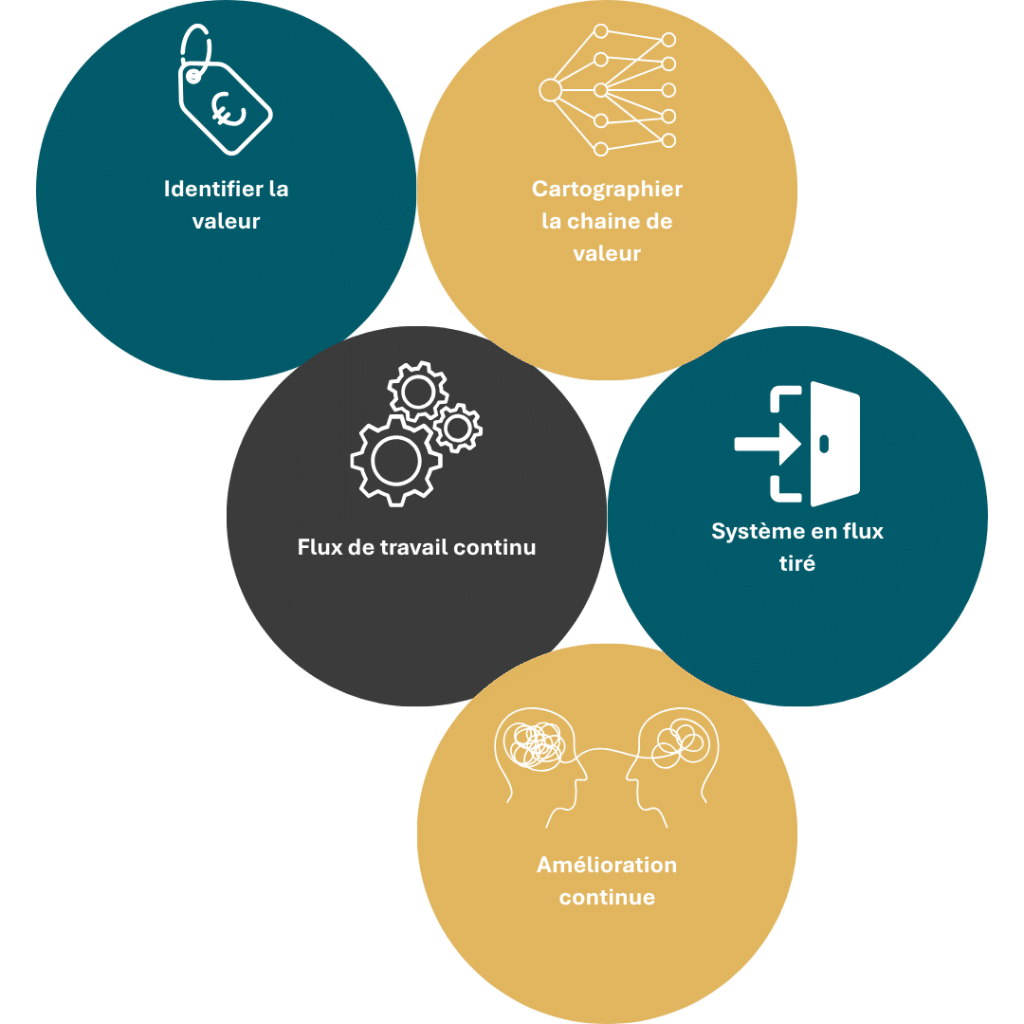

Principe 1: identifier la valeur
Ce principe consiste à identifier précisément les attentes et les besoins du client afin d’orienter l’ensemble des processus vers leur satisfaction.
La démarche comprend donc deux étapes :
- Comprendre les besoins clients ;
- Aligner les processus sur la création de valeur.
Ainsi, tous les efforts sont concentrés sur ce qui a un réel impact.

Principe 2 : Cartographier la chaîne de valeur
La cartographie de la chaîne de valeur consiste à identifier toutes les étapes nécessaires pour délivrer le produit ou service.
Ainsi, cela permet de :
- Visualiser le processus global, les temps d’exécution et d’attente à chaque étape ;
- Détecter les actions inutiles ;
- Optimiser les ressources.
Voici quelques exemples de gaspillage que l’on peut rencontrer lors d’une analyse d’une chaîne de valeur :
- Surproduction ;
- Stock excessif ;
- Défaut et rebuts ;
- Attente de matériel ou décision ;
- Transport et déplacement inutiles ;
- Problème de communication ;
- Réunion inutile.
Cette méthode vise donc à identifier les gaspillages et les inefficacités, et met en avant les opportunités d’amélioration.

Principe 3: Créer un flux de travail continu
- Principe 3 : créer un flux de travail continu
Ce principe permet de minimiser les interruptions entre les différentes étapes et d’améliorer la fluidité du processus.
Pour cela, la décomposition des phases du projet en petites tâches permet une meilleure visualisation du flux de travail et, de cette manière, une meilleure détection des obstacles et des goulots d’étranglement existants.
Ce principe permet souvent de se rendre compte qu’il est nécessaire de se concentrer sur l’optimisation et la diminution des temps d’attente qui sont plus longs que les temps d’exécution.

Principe 4 : établir un système en flux tiré
Un flux tiré est un système de travail où on démarre une tâche une fois la précédente terminée. Ce concept a été mis en place dans les usines afin de réduire les stocks et répondre aux demandes des clients avec précision.
Ce principe est également utilisé dans d’autres domaines comme le développement informatique afin de produire uniquement ce qui est nécessaire, au bon moment. Objectif : éviter les encombrements et les stocks excessifs de travail en attente.

Principe 5 : Amélioration continue
Les quatre premiers principes décrivent le système opérationnel lean. Ils impliquent des changements profonds dans l’entreprise et l’organisation du travail.
Mais la démarche lean n’est pas ponctuelle, elle s’intègre dans un processus itératif où l’amélioration continue est un pilier fondamental.
Elle vise à améliorer progressivement les processus, la qualité et la productivité en impliquant toutes les équipes. Ainsi, plusieurs techniques et outils permettent d’optimiser et d’améliorer les performances.
Quels sont les concepts clés du lean management ?
Le lean Management s’appuie sur plusieurs outils et méthodes permettant d’optimiser les processus, d’éliminer les gaspillages et d’améliorer en continu la performance des organisations.
Voici quelques exemples d’outils utilisés.
Le cycle PDCA ou roue de Deming
La roue de Deming, aussi appelée cycle PDCA (Plan-Do-Check-Act), est une méthode d’amélioration continue qui permet d’optimiser les processus en testant, ajustant et améliorant les pratiques de manière itérative.
Le cycle se divise en quatre étapes.
Plan (planifier) :
Cette première étape consiste à identifier un problème ou une opportunité d’amélioration et à élaborer un plan d’action.
Do (réaliser/développer) :
La deuxième étape permet de tester et d’appliquer la solution à petite échelle.
Check (vérifier/contrôler)
Pendant la troisième étape, l’analyse des résultats obtenus est nécessaire afin de déterminer si la solution est efficace.
Check (vérifier/contrôler)
Si la solution est efficace, celle-ci sera standardisée et généralisée à plus grande échelle. Cette dernière étape va également permettre de capitaliser sur l’expérience acquise pour les améliorations futures.
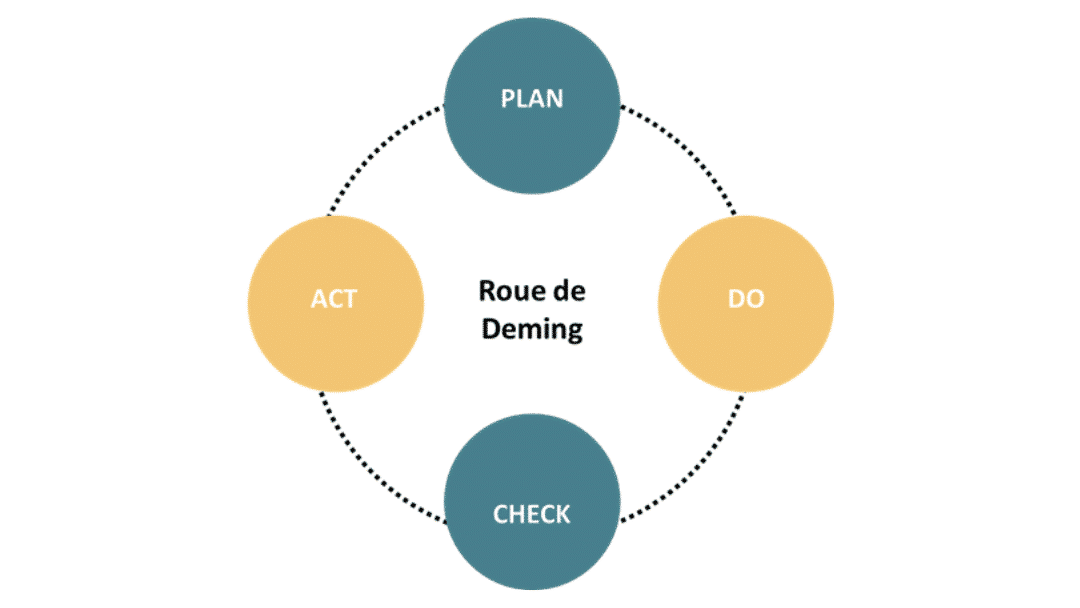
La méthode 5S
La méthode 5S est un outil visant à améliorer l’organisation, la propreté et l’efficacité des espaces de travail. Son objectif est de créer un environnement structuré et optimisé pour réduire les pertes de temps, améliorer la sécurité et favoriser la productivité.
Elle repose sur cinq principes japonais.
Seiri (Trier)
Lors de cette étape, il s’agit d’éliminer toute chose qui n’a pas sa place dans l’espace de travail.
Seiton (Ranger)
Cette étape consiste à ranger les différents outils et matériels nécessaires à la tenue du poste, en recherchant sûreté et efficacité.
Seiso (Nettoyer)
Une fois l’espace de travail dégagé et rangé, il est beaucoup plus facile de le nettoyer. Le nettoyage est l’occasion d’inspecter les installations et de comprendre les sources de salissures afin de traiter les problèmes à l’origine.
Seiketsu (Standardiser)
Cette étape consiste à mener une réflexion collective autour du poste de travail idéal et à définir les règles de fonctionnement de l’équipe. Elle permet également de capitaliser sur le travail déjà mené dans les étapes précédentes pour ne pas avoir à les refaire perpétuellement.
Le livrable de cette étape est la mise en place de standards qui matérialisent la situation normale, l’état de référence.
Shitsuke (Soutenir)
Cette étape a pour objectif de faire respecter l’application des règles définies en équipe pour conserver les acquis et continuer à progresser.
Bien que conçue initialement pour les environnements industriels, elle peut être efficacement appliquée au domaine de l’IT, notamment pour la gestion des infrastructures, du code, des environnements de développement, ou encore des processus ITIL / DevOps.
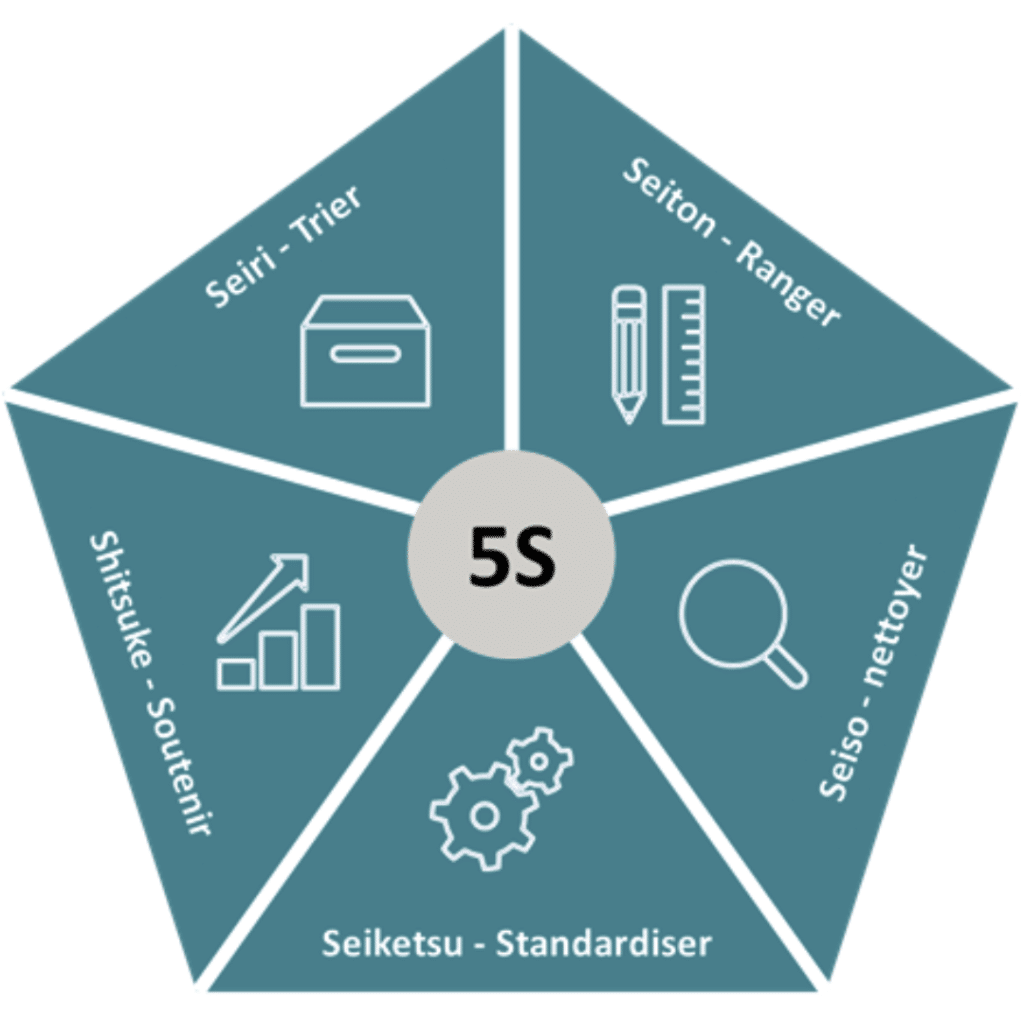
La méthode Kanban
Le Kanban est une méthode visuelle de gestion des flux de travail qui permet d’améliorer la productivité en limitant les gaspillages. Il repose sur un principe de flux tiré, ce qui signifie que la production est déclenchée par la demande réelle plutôt que par des prévisions.
La méthode Kanban repose sur six principes fondamentaux.
Visualiser le flux de travail
La méthode recommande l’utilisation d’un tableau pour représenter les tâches et leur progression. Un tableau Kanban se compose de colonnes représentant les différentes étapes d’un processus (par exemple : « À faire, En cours, Terminé ») et de cartes correspondant aux tâches individuelles.
Limiter le travail en cours
À chaque étape du processus, il convient de fixer un nombre maximal de tâches autorisées, ce qui permet d’éviter les goulots d’étranglement et la surcharge de travail.
Gérer le flux de travail
L’objectif est d’optimiser le passage des tâches d’une étape à l’autre sans interruption. Il faut donc s’assurer que le flux de travail soit fluide en identifiant et corrigeant les éventuels blocages.
Rendre les règles explicites
Il s’agit de partager l’ensemble des règles avec l’équipe afin d’éviter les ambiguïtés. Toutefois, celles-ci doivent rester flexibles et peuvent évoluer en fonction des besoins.
Utiliser des boucles de rétroaction
Les boucles de rétroaction régulières sont essentielles pour ajuster rapidement les processus et maintenir une dynamique d’amélioration continue. Elles permettent d’identifier les problèmes tôt et d’ajuster les priorités.
S’améliorer de manière continue
La méthode favorise une culture de collaboration et d’amélioration continue. L’équipe doit être impliquée dans l’identification et la mise en œuvre des améliorations afin de créer un environnement de travail transparent.
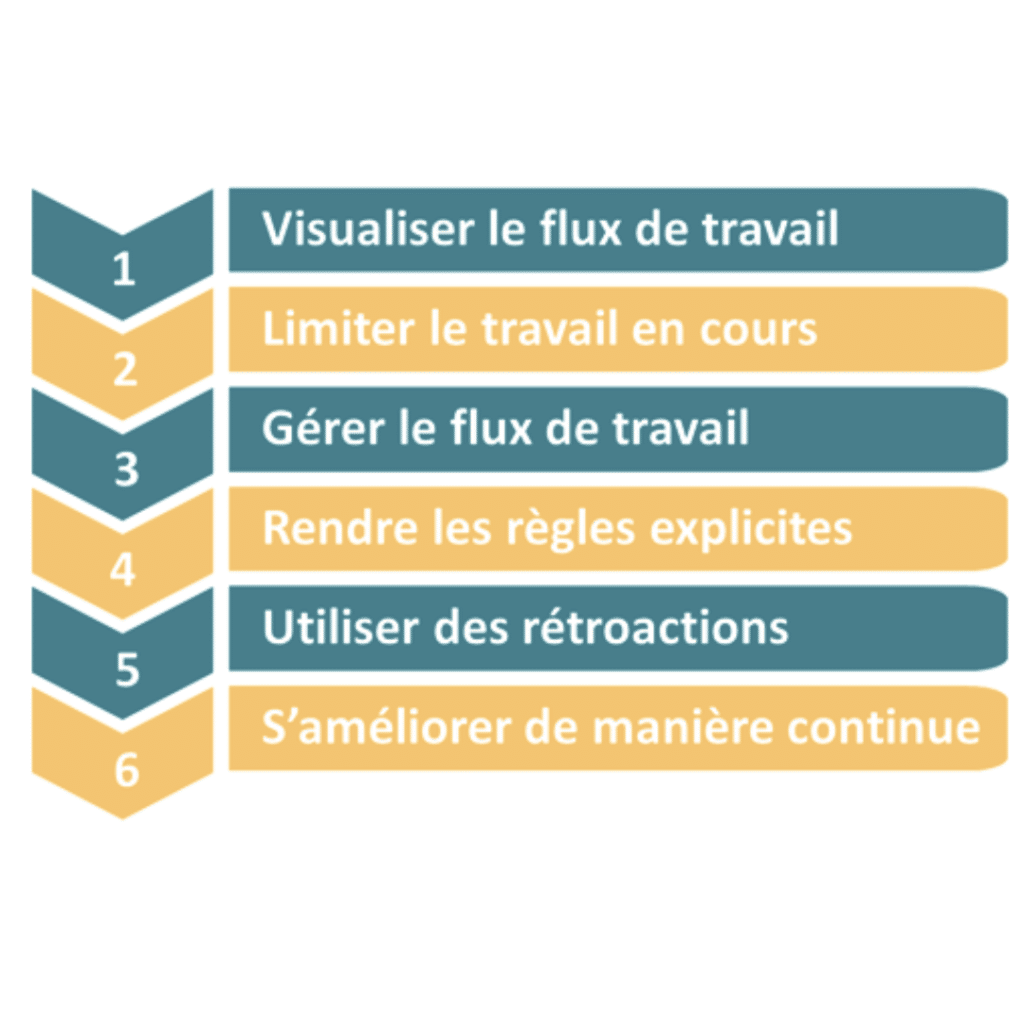
Autres méthodes
D’autres méthodes existent également telles que les méthodes SMED, Six Sigma, VSM ou Kaizen.
Conclusion
Le lean management présente ainsi de nombreux avantages, notamment une réduction des coûts et une meilleure productivité, mais surtout une amélioration de la qualité des produits et services. C’est pourquoi cette méthode s’est imposée comme une alternative aux méthodes classiques et représente aujourd’hui un levier important pour les entreprises qui souhaitent gagner en flexibilité et en efficacité face aux défis actuels du marché.
Mais comment les principes lean peuvent-ils être appliqués à des environnements moins prévisibles, comme la gestion de projet ? Le lean peut-il réellement répondre aux défis de flexibilité, d’incertitude et de collaboration interdisciplinaire que rencontrent aujourd’hui les chefs de projet ? Nous tenterons de répondre à ces questionnements dans un second article.
Pas encore de commentaires